UNDERSTANDING PROCESSES
REDUCE WASTE
Process optimization refers to the process of improving workflows to increase efficiency, productivity and quality. It involves analyzing and redesigning existing processes to identify bottlenecks, reduce waste and maximize overall performance. Our process optimization can take place in several steps:
- Process analysis: This step involves a detailed examination of the existing process. Data is collected on the process, resources, time, and outcomes. The goal is to understand the process flow and identify weak points.
- Bottleneck identification: Bottlenecks are areas in the process that affect performance and efficiency. By analyzing the data from the first step, bottlenecks can be identified. These can be, for example, slow machines, bottlenecks in material procurement or bottlenecks in communication between different departments.
- Identify waste: Process optimization aims to reduce waste. These include, for example, unnecessary waiting times, excessive movements, overproduction or defects. By identifying these wastes, actions can be taken to eliminate or minimize them.
- Process redesign: Based on the analyses and identification of bottlenecks and waste, the process is redesigned. Improvements and changes are made to increase efficiency. This can mean, for example, redistributing tasks, introducing new technologies or optimizing communication channels.
- Implementation: The revised processes are implemented. This includes training employees, providing the necessary resources, and implementing new systems or technologies.
- Monitoring and control: After implementation, the optimized processes are monitored and controlled to ensure that the targeted improvements are achieved. Key figures and performance indicators can be used to evaluate the effectiveness of the optimizations and make further adjustments if necessary.
Process optimization is a continuous process that requires regular reviews and adjustments to ensure that workflows are always at their most efficient.
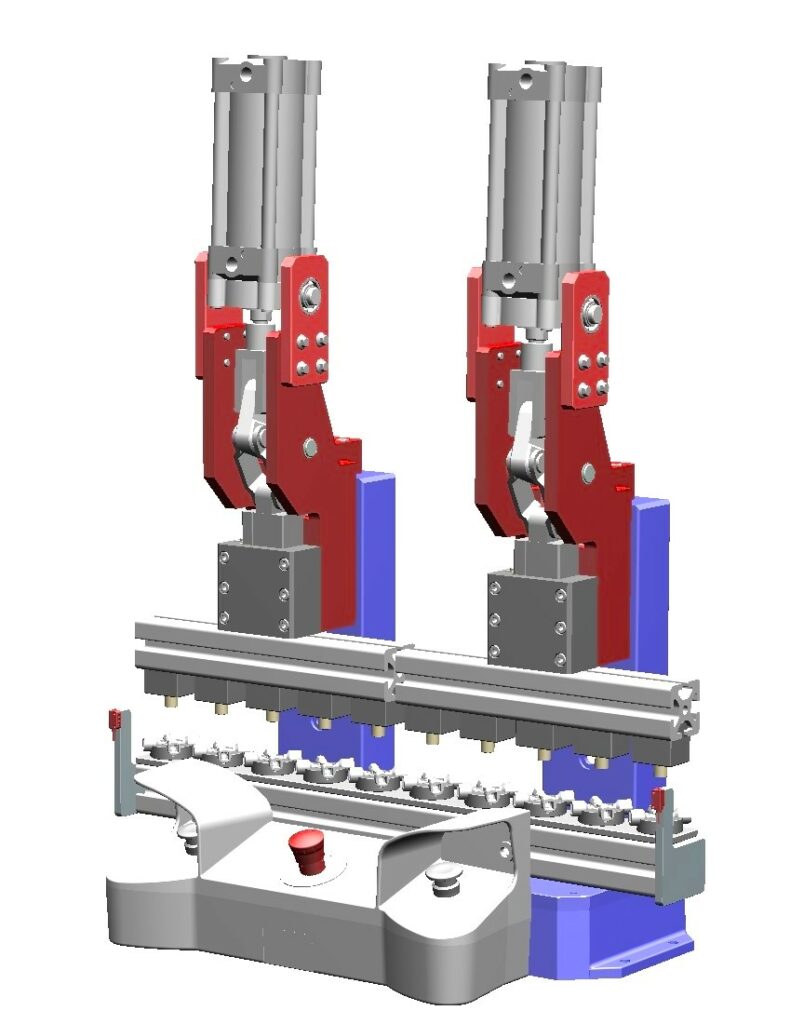